3. Components of a thermal power system
So far we have introduced the concept of thermal power system and the concept of a working fluid. In this section we will take a look at the four main components that make up this these systems, namely a pump or compressor, an expander and two heat exchangers.
As a recap, a thermal power system is composed of four distinct process, namely compression, heating, expansion and cooling, that are coupled together to form the system. A working fluid is the fluid that undergoes each of these processes in turn.
Within these webpages, we will focus on two of the main types of thermal power system, which are the Brayton cycle and the Rankine cycle. These cycles are widely used for power generation, and form the basis of gas power plants and steam power plants respectively. In both of these systems, each of the four processes is obtained by a different component. Thus, a simple thermal power system can be thought of as the combination of four components that each have a particular job to do. It is worth noting that there do exist more complex systems that utilise a larger number of components, but these systems are largely just variations on this basic system.
The difference between the Brayton cycle and the Rankine cyice is the working fluid that is used. In a Brayton cycle, the working fluid is air, and thus air is compressed, heated, expanded and then cooled. However, in a Rankine cycle the working fluid is typically water, which during the heating process, is converted from a liquid to a gas. Thus, in a Brayton cycle the compression process must compress a gas, whilst in a Rankine cycle the compression process must compress a liquid, which require slightly different components.
Thus, the four components that make up either a Brayton and Rankine thermal power system are as follows:
- a compressor or pump to undertake the compression process
- a heat exchanger to undertake the heating process
- an expander or turbine to undertake the expansion process
- and another heat exchanger to undertake the cooling process
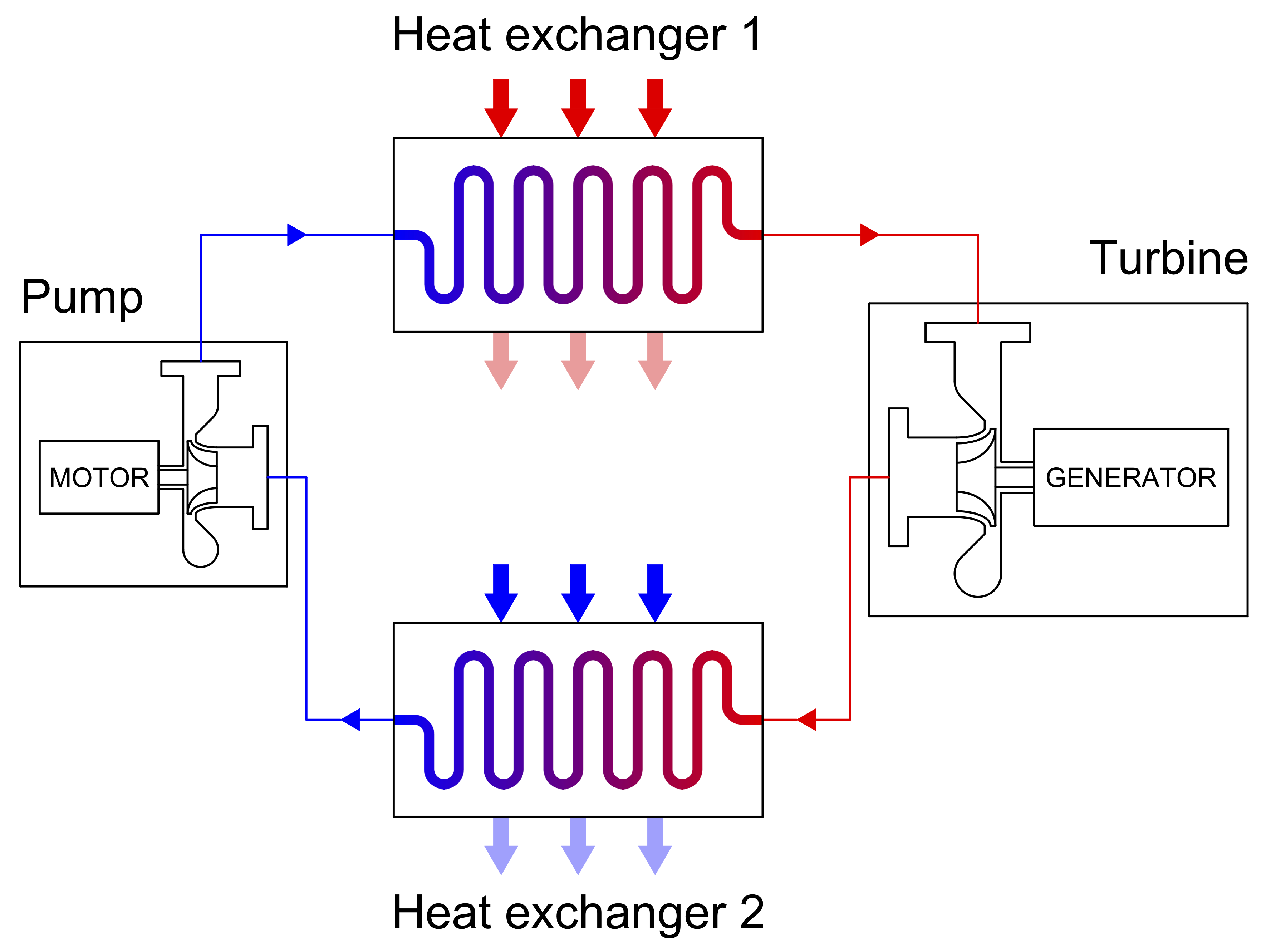
Diagram showing the components that make up a basic thermal power system (in this case a Rankine cycle).
A compressor or pump is used to compress the working fluid. The key difference between a compressor and a pump is that a compressor is used to compress a gas, whilst a pump is used when the fluid undergoing the compression is a liquid. Thus, in a Brayton cycle the compression process is achieved using a compressor, whilst in a Rankine cycle, the compression process is achieved using a pump. Both compressors and pumps achieve an increase in the pressure of the fluid by the addition of energy to the fluid. In practical terms, this means using an electric motor to drive a shaft that causes the rotor of the pump or compressor to rotate, thus causing the movement, and pressure increase, of the fluid.
An expander is the term used to describe the component that expands the working fluid and thus generates the useful energy that can be used directly or converted into electricity. Unlike the compression process, the fluid undergoing the expansion process is nearly always a vapour (with the exception of two-phase expanders - more on this later…). As such, there is no need to distinguish between a liquid expander and a vapour expander. An expander operates in the reverse of a compressor or pump. In this case, the expansion of the fluid causes the rotor of the expander to rotate, which, in turn, drives a shaft that can be connected to an electric generator. The result of this is the generation of electricity. A turbine or turboexpander is a particular type of expander that uses blades that are mounted onto the rotor shaft to achieve the expansion process. One of the most familiar types of turbine is probably a wind turbine, although turbines come in a variety of shapes and sizes, depending on the application. Other applications for turboexpanders include aircraft engines, or turbochargers within cars. Turboexpanders are by far the most common type of expander used within thermal power systems.
A heat exchanger is the general term used for a device that transfers heat from one fluid to another. One of the most familiar examples is probably a domestic radiator, which transfers heat from the hot water supplied by your boiler to the ambient air within your house. In this application there are two fluid streams (the hot water and the ambient air) which transfer heat between each other through a solid metal wall. The heat exchangers within a thermal power system do exactly the same. For example, in a fossil-fuel power plant the heat released by the burning of the fuel is transferred to the working fluid using a heat exchanger that transfers heat from the hot gases generated by the combustion of the fuel, to the working fluid. Likewise, in the same system, another heat exchanger is used to transfer heat from the working fluid to the ambient surroundings during the cooling process.